Everything about
Application of Biocompatible Resins
Everything about
Application of Biocompatible Resins
Everything about Application of Biocompatible Resins
Whether we talk about the health industry, dentistry or wearables, biocompatible resins are paramount to ensure the health and comfort of the wearer. In this article, we take a bird’s-eye-view on most common industries and applications, including:
- Dental Biocompatible 3D Printing Applications
- Medical Biocompatible 3D Printing Applications
- Wearable Biocompatible 3D Printing Applications
What Are Biocompatible Resins?
Biocompatible resins are materials that are designed to be compatible with living tissues and biological systems. It's crucial to note that the term "biocompatible" doesn't imply a one-size-fits-all characteristic.
Contrary to public belief, specific raw materials or raw material classes cannot claim to be biocompatible. Rather, the final printed part needs to be tested to get the final approval. In the US, companies even need to FDA-qualify the same 3D printing resin on different printers.
Therefore, different materials may have varying degrees of biocompatibility depending on factors such as:
- Degree of modification
- Application context
- Degree of degradation
- Compliance with standards
Biocompatible resins are used in various applications, particularly in the medical and healthcare fields, where they come into contact with the human body.
The key characteristic of biocompatible resins is therefore their ability to interact with biological systems without causing harm or adverse reactions.
Understanding Biocompatibility in 3D Printing
To truly appreciate the value of biocompatible resins, it’s important to understand what biocompatibility means in a 3D printing context. According to ISO 10993-1, biocompatibility is defined as:
"The ability of a medical device or material to perform with an appropriate host response in a specific application."
In practical terms, this means that a biocompatible 3D printing material must integrate seamlessly into its intended application without causing adverse effects. It’s a common misconception that biocompatibility means "completely risk-free." Instead, it signifies that the material has been rigorously tested and deemed safe within specific usage conditions
Several key factors determine the biocompatibility of 3D printing resins, including:
- Material Composition – The chemical formulation of the resin and its interaction with biological tissues.
- Processing & Post-Curing – Proper cleaning, curing, and sterilization significantly impact the final biocompatibility of the material.
- Application-Specific Testing – The level of testing required depends on how and where the material will be used, whether for short-term external applications or long-term medical implants.
With advancements in 3D printing technology, modern biocompatible resins are offering unmatched precision, durability, and safety. These materials are playing a pivotal role in dental aligners, surgical guides, and patient-specific implants, transforming the way healthcare professionals approach personalized treatments.
By leveraging high-quality biocompatible 3D printing materials, manufacturers can enhance product safety, streamline production, and contribute to groundbreaking medical innovations
The Role of Standards in Biocompatible 3D Printing Materials
The growing demand for biocompatible resins in 3D printing for medical and dental applications highlights the importance of meeting strict industry standards. These materials are specifically formulated to ensure safety, reliability, and long-term performance, making them ideal for medical implants, dental prosthetics, and other healthcare applications.
One of the key questions manufacturers face is: How can biocompatible resins be certified as safe for long-term use? The answer lies in comprehensive compliance testing. International standards, such as ISO 10993, provide a structured framework for evaluating biocompatible 3D printing materials, ensuring they meet stringent safety and regulatory requirements.
However, achieving full compliance requires more than just passing a single test. While many suppliers claim adherence to ISO 10993, it is crucial to specify which of its 20+ sections apply to a given material. Transparent documentation helps manufacturers and medical professionals make informed decisions about material selection and patient safety.
As 3D printing continues to revolutionize the medical field, ensuring biocompatible resins meet evolving safety and performance expectations is essential. Responsible manufacturers are already taking steps to enhance transparency, refine certification processes, and provide high-quality materials that support innovative and life-changing applications.
Industries and Applications of Biocompatible Resins
The following section describes applications, which are made of biocompatible resins.
Dental Biocompatible 3D Printing Applications
Biocompatible materials play a pivotal role in various dental applications, ensuring compatibility with oral tissues and minimising adverse reactions.
- Dental Splints: Night guards are often used to alleviate issues like teeth grinding and jaw clenching and benefit from biocompatible resins or thermoplastics. These materials not only provide comfort but also reduce the risk of irritation or allergic reactions in the delicate oral environment.
- Hybrid dentures: Incorporating both traditional and modern materials, hybrid dentures utilise biocompatible polymers and metals for their base structures. These materials offer durability and compatibility with oral tissues, enhancing patient comfort and long-term wearability.
- Ceramic crowns: Praised for their natural appearance and biocompatibility, ceramic crowns are commonly used to restore damaged or decayed teeth. Their ability to mimic natural tooth enamel while seamlessly integrating with surrounding tissues makes them a preferred choice in restorative dentistry.
Medical Biocompatible 3D Printing Applications
Biocompatible materials are used in a myriad of medical applications, ensuring compatibility with the human body and facilitating safe and effective treatments.
- Endoprostheses: Joint replacements and implants rely on biocompatible metals like titanium and medical-grade polymers to seamlessly integrate with surrounding tissues, promoting healing and restoring function without triggering adverse reactions.
- Epitheses: These prosthetic devices are designed to replace missing facial features and utilise biocompatible materials to mimic natural skin and tissues, which offers patients both aesthetic restoration and functional improvement with minimal risk of rejection.
- Endoluminal stents: Devices used to support narrowed or weakened blood vessels or gastrointestinal passages, typically crafted from biocompatible metals or polymers. These materials ensure proper vessel support and promote tissue healing without causing inflammation or thrombosis.
- Maxillofacial guides: Essential tools in reconstructive and corrective surgeries of the jaw and face, fabricated from biocompatible resins or plastics. These guides assist surgeons in precise anatomical alignment and facilitate optimal surgical outcomes while minimising trauma to surrounding tissues.
Wearable Biocompatible 3D Printing Applications
The integration of biocompatible materials and 3D printing technology has led to new wearable applications, like various 3D-printed wearable devices, that prioritise user comfort, safety, and functionality.
- Sensors: Sensors embedded in wearable devices, such as fitness trackers and health monitors, benefit from biocompatible materials that ensure skin contact without causing irritation or allergic reactions. These sensors can continuously monitor vital signs, activity levels, and other health metrics, offering valuable insights for both medical and personal wellness applications. Similarly, 3D printing in the automotive industry is revolutionizing sensor technology by enabling the creation of lightweight, durable, and customizable components that can be seamlessly integrated into vehicles for enhanced performance and safety.
- Wearable technology: Devices, including smartwatches, augmented reality glasses, and medical wearables, rely on biocompatible materials to enhance user experience and promote long-term wearability. Biocompatible polymers and coatings ensure that these devices can be worn comfortably for extended periods without compromising skin health.
- Sports equipment: Equipment, such as custom mouth guards and protective gear, utilises biocompatible materials to provide athletes with optimal comfort and protection during training and competition. These materials can withstand impact forces while conforming to the wearer's body contours, minimising the risk of injury.
- Fashion accessories: Ranging from 3D printing for jewellery to eyewear, biocompatible materials offer both style and safety. Biocompatible resins and metals allow designers to create intricate designs that can be worn close to the skin without causing irritation or discomfort.
Methods of Biocompatible Resins 3D Printing
Several 3D printing methods can be employed to create biocompatible products. Stereolithography (SLA), Digital Light Processing (DLP) as well as Material Jetting belong to the most popular printing methods.
- Stereolithography (SLA) employs UV curable resin for 3D printing, where a UV laser selectively cures the resin layer by layer, solidifying it into the desired shape. SLA offers high resolution and surface finish, making it suitable for intricate biomedical models to meet stringent requirements. For even greater precision and complexity in 3D printing, techniques like 3D Microfabrication can further enhance the capabilities of SLA, especially in biomedical applications.
- Similar to SLA, Digital Light Processing (DLP) utilises a digital light projector to cure liquid resin layer by layer. However, DLP projects an entire layer simultaneously, speeding up the printing process. Biocompatible resins for DLP should exhibit low shrinkage and high accuracy, making them suitable for dental applications and surgical guides.
- Material Jetting, on the other hand, employs inkjet printing to deposit layers of 3D printing photopolymer resin. It offers multi-material printing capabilities and can produce parts with varying mechanical properties. Biocompatible resins are used in applications such as hearing aids and anatomical models for surgical planning.
Create High-Quality Products with RAHN’s Resins
Creating medical products requires thorough research to pass all legal requirements. RAHN supports you during the entire process to create valuable and competitive products. Contact us to find out more about our raw materials for 3D printing and a wide range of other industries.
Your personal contact
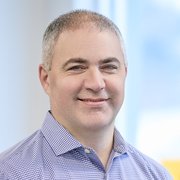
Christopher Cocklan
3D Printing Business Development Manager EnergyCuring
RAHN USA Corp.